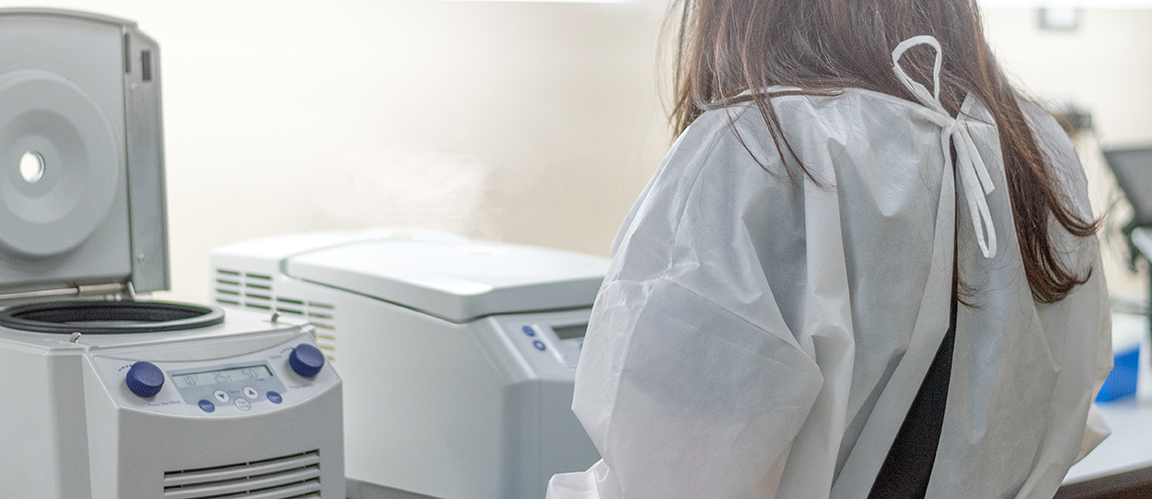
Creating a Global Transformation with TrackWise Digital®
SGS Life Sciences: Creating a Global Transformation with TrackWise Digital
How does a venerable inspection and testing brand with more than 2,600 offices around the world foster a global transformation of its Life Sciences division? By focusing on holistic collaboration, built on the robust TrackWise Digital quality management system (QMS) platform.
For nearly 150 years, SGS Group, headquartered in Geneva, Switzerland, has provided inspection, verification, testing, and certification services for a variety of industries. With more than 94,000 employees and annual revenue of over CHF 6.5 billion (USD 6.8 billion), the company’s customer-centric culture and dedication to quality are integral to its success and reputation.
Nearly one-third of the company’s revenue comes from its Life Sciences division. SGS Life Sciences provides analytical laboratory and clinical research services for agricultural, pharmaceutical and biotechnology, food and beverage, and other nutrition and health industries. These services span manufacturing stages from preclinical to trade distribution.
THE PROBLEM: DOCUMENT-CENTRIC SYSTEMS COULDN’T MEET MODERN DEMANDS
Like many life sciences organizations, SGS Life Sciences’ quality environment was heavily paper-based and document-centric. Between the SOPs, forms, and reports generated for change control processes, deviation management, compliance requirements, and so on, the division’s operations and quality teams were creating, managing, and storing more than 25,000 Unique items.
A Growing Burden
The high volume of paper across Life Sciences’ 17 global testing laboratories had become a burden to the division’s quality efforts:
- Transcribing and verifying data took up an inordinate amount of time.
- The potential for transcription errors introduced real risk.
- The high volume of paper conflicted with SGS’s commitment to environmental sustainability.
- Both customers and regulatory authorities increasingly challenged paper systems as inferior to digital records keeping.
A Vision for Growth
The OneVision initiative aimed to mitigate these issues. By transitioning to a fully digital network, SGS hoped to interconnect people, systems, and laboratories with a focus on business excellence. The success of the effort depended on implementing a state-of-the art digital platform that would enable Life Sciences to achieve several ambitious goals:
- Optimize and streamline processes and workflows to improve efficiencies, capacity, turnaround times, and customer service.
- Reduce the division’s environmental impact by slashing the need for paper use and storage.
- Centralize and digitize the network’s knowledge and communications platforms to improve communications, both internally and across its customer, supplier, and partner networks.
Chambers, who leads SGS Life Sciences’ business development strategy and growth plan for analytical testing labs across North America, Europe, and Asia, was tasked with launching the OneVision initiative.
- Part of this effort involved interfacing the Life Sciences laboratories’ instruments with SGS’s laboratory information management system (LIMS).
- The division also needed to move to electronic, automated data collection by implementing electronic lab notebook (ELN) and laboratory execution system (LES) systems.
- Life Sciences needed to transform the division’s document-centric quality, document and training management systems (QMS, DMS, and TMS) to digital automated workflows and records.
THE SEARCH BEGINS
Chambers and a team of about 30 Life Sciences subject matter experts, quality professionals, and business leaders began by reviewing product demos and participating in deep-dive solution workshops and functional assessments from a shortlist of potential QMS vendors.
“We wanted to eliminate our paper-based quality records. But gaining full traceability and visibility of all quality events, both locally and globally, was also a challenge for us,” he says.
THE SOLUTION: A HOLISTIC VISION, SUPPORTED BY TRACKWISE DIGITAL
TrackWise Digital’s powerful Salesforce platform and the team’s extensive expertise in the life sciences industry, made an impression on Chambers and the SGS Life Sciences team. Chambers notes that the decision to use TrackWise Digital was on a variety of factors:
- An intuitive user interface and easy-to-navigate dashboards made it simple to locate documents — locally, regionally, and globally
- Better customer support than comparable solutions, including help building dashboards with the metrics SGS wanted
- Clearly defined processes — important for rolling out a global system across 17 sites
- Strong reporting options, including trending reports.
- A comprehensive module set that enables management of quality, complaints, documents, training, supplier quality, and CAPA
- Comprehensive audit management features that enable direct submission of audit replies — making life easier for companies like SGS, which hosts about 400 client audits and significant health authority inspections each year
- An outstanding reputation and high use in the Life Science industry, including regulators and many of SGS’s partners
- A robust platform that could form a foundation for OneVision’s LIMS, ELN, and LES systems
TrackWise Digital QuickStart
Because SGS had an ambitious timeline for its OneVision rollout, Chambers told the TrackWise Digital team that he wanted no more than 10% customization of the QMS.
To speed deployment, Chambers chose Quality Management QuickStart, a packaged deployment offering with a predetermined timeline and methodology. SGS also implemented Quality Process Accelerators — preconfigured templates and workflows based on best practices identified through decades of industry experience — to ensure fast compliance with ICH, GMP and GLP regulations and guidance.
An Ambitious Roadmap
The TrackWise Digital team worked with Chambers and the SGS Life Sciences team to meet an aggressive roadmap.
“We are very proud of what we’ve achieved through our collaboration with the TrackWise Digital team, working together with clear expectations,” says Chambers.
Testing and deployment of TrackWise Digital began in March 2019, with the QMS going live at SGS’s Chicago lab site within 3 months. TrackWise Digital QMS was quickly rolled out to 11 more sites across seven countries by the end of 2019, with more sites scheduled for deployment throughout 2020.
Following full QMS rollout, SGS plans to finalize its pilot of the TrackWise Digital DMS and TMS modules. The company will complete a bulk upload of related documents and a global rollout of these modules in early 2021.
By then, notes Chambers: “We’ll have eliminated more than 25,000 paper forms and SOPs. That’s significant and will hopefully go a long way toward reducing replication, as well as transcription and other human-introduced errors. This change is truly helping us embrace a ‘right first-time’ culture.
“This timeline is possible only with a cloud-based SaaS solution like TrackWise Digital,” he says. “This type of digital system is increasingly becoming the enterprise best practice.”
THE RESULTS: FAST ALIGNMENT AND “INSTANT BENEFITS”
With the help of TrackWise Digital, SGS’s OneVision initiative is delivering instant benefits to Life Sciences’ employees and customers. The system is working well and receiving positive feedback from both Life Sciences lab sites and clients.
SGS is also receiving positive feedback from clients. “Onsite audits over the past year have been positive about leveraging TrackWise Digital, and virtual internal and external audits are easy to maintain through review of eQMS data and scanned documents. Plus, the solution’s anywhere/anytime capabilities have better positioned us to continue operating at the highest state of quality and integrity during the COVID-19 crisis.”
Chambers says that value stream mapping conducted mid-2019 — just weeks after deployment — already showed significant improvement in cycle time for quality events.
“We conducted a value stream mapping analysis at our Lincolnshire site shortly after go-live and received good indications for improvements in cycle time over the previous paper-based process,” he notes. “We’re currently considering a second assessment at another site.
“The solution certainly delivered the quick business improvement I wanted!” he says.
By streamlining the input processes and reducing unnecessary paperwork and replication, the solution has increased efficiency. And the integrated, centralized ecosystem and TrackWise Digital support makes it easier for affiliates to access expert support from global industry experts. Best of all, the introduction of TrackWise Digital has been nearly seamless for the Life Sciences division, which has needed to operate as usual and maintain annual KPIs during the rollout.
“TrackWise Digital has enabled me to introduce more quick, sustainable results within our complex working environment,” explains Chambers. “We’ve been able to use the solution to drive culture change within our organization. Our OneVision project encompasses TrackWise Digital as a foundation to that culture change within our strategic business unit.”
Now, TrackWise Digital dashboards provide live access to quality-related KPIs, eliminating the need for manual KPI reporting each month. For the first time, Chambers says, the division can globally view and interactively work with all facilities on a daily basis. A new level of visibility into specific quality events, review trends, and reports enable greater insight for multiple stakeholders, regardless of their location. As a result, the Life Sciences Quality team can more easily collaborate on important Good Manufacturing Practice (GMP) decisions, root cause analysis, and risk mitigation.
Customized reporting capabilities enable the team to pinpoint specific processes and problem areas. As a result, the division can quickly take action on effective CAPA processes, to the benefit of SGS’s customers.
And especially important in the era of COVID-19, TrackWise Digital makes it easy to conduct virtual internal and external audits through anywhere, anytime, cloud-based access to the division’s QMS data.
He looks forward to completing the rollout of TrackWise Digital’s DMS and TMS modules, the next step in the division’s OneVision evolution.
“TrackWise Digital is the foundation of the vision that we’re driving at SGS,” says Chambers. “The solution underpins every other change that we’re making. Yes, we have a CRM solution, two LIMS systems, and a global quotation tool in addition to our QMS, DMS, and TMS system. But all that has been built on a strong, sound cornerstone: The TrackWise Digital platform.”