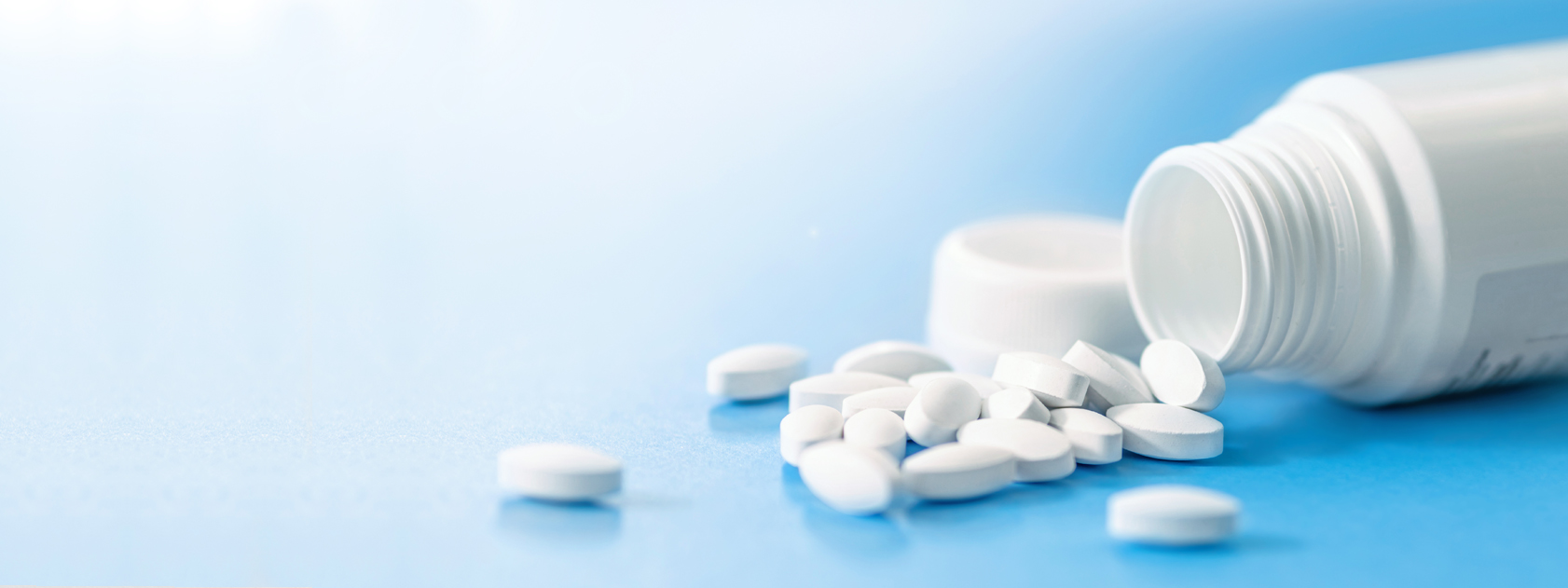
Natco Pharma Transforms Quality Management with TrackWise®
Natco Pharma Transforms Quality Management with TrackWise
Natco Pharma, a leading pharmaceutical company, was incorporated in Hyderabad in 1981 with an initial investment of INR 3.3 million. With a modest beginning of operations as a single unit with 20 employees, Natco today has seven manufacturing facilities spread across India with dedicated modern research laboratories, capabilities in New Drug Development and more.
The Natco family currently consists of around 5,000 employees. The company is consistently ranked among fastest growing pharmaceutical companies in India and is well recognized for its innovation in Pharmaceutical R&D.
Natco selected TrackWise to transform its approach to quality management.
THE OPPORTUNITY
Transforming a Legacy Approach to Quality Management 
Before implementing TrackWise, one of Natco’s top challenges was its legacy approach to managing quality. This process was tedious as it required daily follow ups with the cross functional teams for the closure of all activities. This proved to be inefficient and was prone to compliance challenges. For example, all quality documents had to be created manually on request, resulting in a time-consuming process. Paper records were manually distributed across all teams, creating a delay in completing activities and resulting in risk of being lost during handling.
Tracking the review, closure and escalation of all activities also proved to be tedious and collaboration was hindered because physical documents had to be forwarded or shared for signatures.
This paper-based approach resulted in a lack of readiness to face audits. Natco needed a robust system that would enable the company to have control over its processes, was compliant with regulations like 21 CFR Part 11 and proven in the industry.
Throughout the evaluation process, Natco went through several activities to choose the best software and implementation partners.
When it came to identifying an implementation partner, a lot of evaluation was done to find the best fit, which brought it to Navitas Life Sciences. Navitas has a breadth of experience in TrackWise implementations and specialized knowledge in QMS processes, making it the ideal partner. Navitas was able to rapidly perform the implementation without compromising quality.
For the software partner, Natco was looking for a vendor that could combine all quality processes in a centralized solution, automate those processes and include industry best practice workflows that were easily customizable and user friendly.
It found these capabilities in the TrackWise quality management solution.
THE SOLUTION
Making the Switch from Manual to Automated
The implementation consisted of highly interactive workshops, involving discovery sessions with process champions. Navitas provided robust, industry-standard workflows to Natco to enable better quality interaction with all cross functional teams. These workshops also helped Natco understand the challenges with manual processes and where automation would alleviate these challenges. Natco’s processes were designed leveraging industry standard best practices and internal standard operating procedures (SOPs) to drive those processes. It designed lean and simple business processes and harmonized them across all sites with TrackWise.
“It was very easy to extend TrackWise to other units across the company so all units are under the same quality system,” said Reddy. “This provides better control over the quality system and upper management will have better visualization of what’s happening across all units, from one dashboard in a single location.”
Natco ensured on time delivery by using a phased implementation approach that took place in three phases. The first phase consisted of the system go live and user adoption and included incidents, temporary change control, investigations, corrective and preventive action (CAPA), and child workflows including extensions, effectiveness checks, and action Items. Training was a key aspect of success here. Navitas provided training and workshops to ensure key users were thoroughly trained on how to use the TrackWise system. A train the trainer approach was used to help with early adoption. After the successful implementation of TrackWise by Navitas, the manual system and processes were discontinued and made obsolete.
THE RESULTS
Greater Productivity, Insights and Compliance
Since implementing TrackWise, Natco has seen an increase in productivity and has cut down on the number of resources needed to manage their QMS. This enables employees to focus on other mission-critical activities. With visibility into the status of all documents, Natco can now track which documents are pending and for how long, so the company can move onto the next step without delays.
Any authorized user can log in to the system and check the status in real time, empowering employees at all levels and providing visibility into tasks that need to be completed across the cross functional team.
TrackWise has enabled Natco with an efficient means for reporting on quality data, in turn empowering the company to make actionable business decisions and gain anytime audit readiness.
Reddy considers audit management to be one of the best features, explaining, “robust audit trails will give a clear picture on the changes that are being made and why.”
LOOKING AHEAD
Natco has a well laid out plan to achieve total quality transformation across its business. It has successfully completed phase one—phases two and three will be conducted throughout the remainder of the year.
Phase two will include the implementation of market complaints handling and change control and Phase three will consist of audit management and out of specification (OOS). Natco plans to have both phases completed by November of 2021.
“As we keep building on the data in TrackWise it will be useful for us to take it further in creating trends and metrics,” said Reddy. Natco continues to get acquainted with the system and at the click of a button can get insight into what’s pending and why and compare trends.
The Natco team is pleased that this data is easy to prepare and is readily accessible for audits.